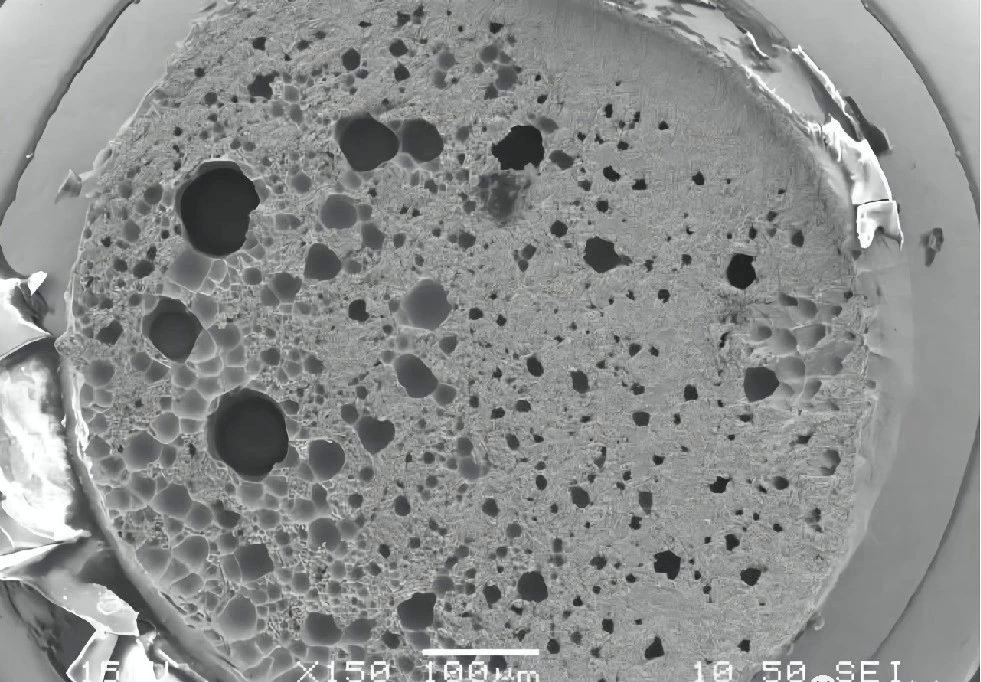
1 Вступ
У збірці друкованої плати паяльна паста спочатку друкується на припойній площадці друкованої плати, а потім прикріплюються різні електронні компоненти. Нарешті, після печі оплавлення олов’яні кульки в паяльній пасті розплавляються, а всі види електронних компонентів і паяльна площадка друкованої плати зварюються разом, щоб реалізувати збірку електричних субмодулів. Технологія поверхневого монтування (sMT) все частіше використовується в пакувальних продуктах високої щільності, таких як пакети системного рівня (siP), пристрої з кульковою решіткою (BGA) і електросхеми, квадратні плоскі пакети без контактів (quad aatNo-lead, відомі як QFN). ) пристрій.
Через характеристики процесу зварювання пастою та матеріалів після зварювання оплавленням цих пристроїв з великою поверхнею припою в зоні зварювання з’являться отвори, що вплине на електричні властивості, теплові властивості та механічні властивості продукту. навіть призвести до виходу з ладу продукту, отже, для покращення паяльної пасти оплавлення порожнини зварювання стало процесом і технічною проблемою, яку необхідно вирішити, деякі дослідники проаналізували та вивчили причини BGA порожнини зварювальної кульки припою та наданих рішень для покращення, звичайний процес зварювання оплавленням паяльною пастою, площа зварювання QFN більше 10 мм2 або площа зварювання більше 6 мм2 не має рішення для оголеного чіпа.
Використовуйте зварювання преформ припоєм і зварювання у вакуумній печі з зворотним холодильником, щоб покращити зварний отвір. Збірний припій вимагає спеціального обладнання для точкового флюсу. Наприклад, чіп зміщується та серйозно нахиляється після того, як чіп поміщається безпосередньо на збірний припій. Якщо чіп для монтування флюсу є оплавленням, а потім точкою, процес збільшується на два оплавлення, а вартість попередньо виготовленого припою та флюсового матеріалу значно вища, ніж паяльна паста.
Вакуумне рефлюксне обладнання є дорожчим, вакуумна ємність незалежної вакуумної камери дуже низька, вартість невисока, а проблема бризок олова є серйозною, що є важливим фактором у застосуванні високої щільності та малого кроку продуктів. У цій статті на основі звичайного процесу зварювання оплавленням паяльною пастою розроблено та представлено новий вторинний процес зварювання оплавленням, щоб покращити зварювальну порожнину та вирішити проблеми з’єднання та розтріскування пластикового ущільнення, спричинені зварювальною порожниною.
2 Друк паяльною пастою, порожнина зварювання оплавленням і виробничий механізм
2.1 Зварювальна порожнина
Після зварювання оплавленням виріб було перевірено рентгенівським промінням. Отвори в зоні зварювання зі світлішим кольором виявилися через недостатню кількість припою в зварювальному шарі, як показано на малюнку 1
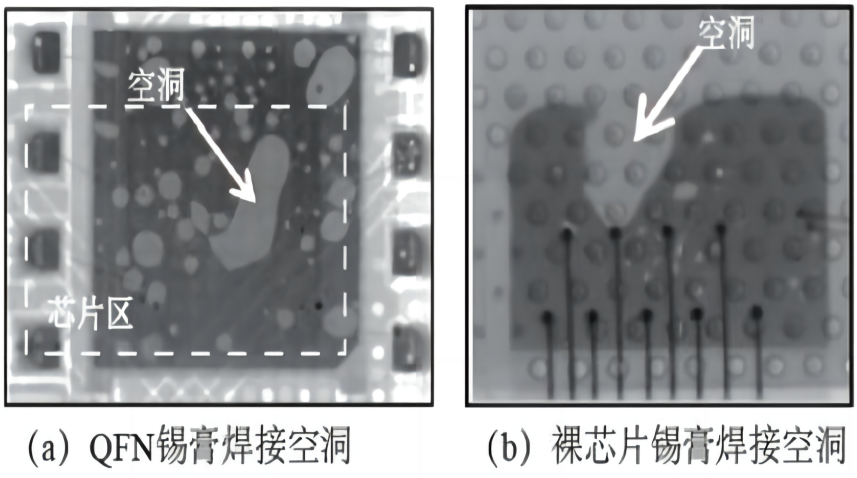
Рентгенологічне виявлення бульбашкового отвору
2.2 Механізм утворення зварювальної порожнини
На прикладі паяльної пасти sAC305 основний склад і функції наведено в таблиці 1. Флюс і олов’яні кульки з’єднані разом у формі пасти. Співвідношення ваги олов'яного припою до флюсу становить приблизно 9:1, а об'ємне співвідношення - приблизно 1:1.
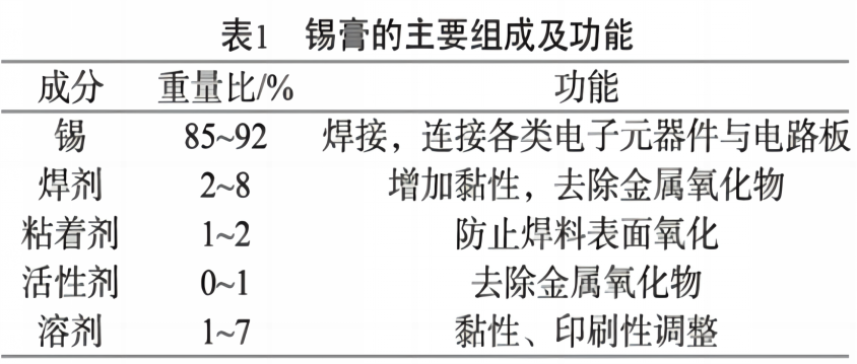
Після того, як паяльна паста надрукована та змонтована з різними електронними компонентами, паяльна паста проходить чотири стадії попереднього нагріву, активації, кипіння та охолодження під час проходження через піч із зворотним холодильником. Стан паяльної пасти також відрізняється при різних температурах на різних етапах, як показано на малюнку 2.
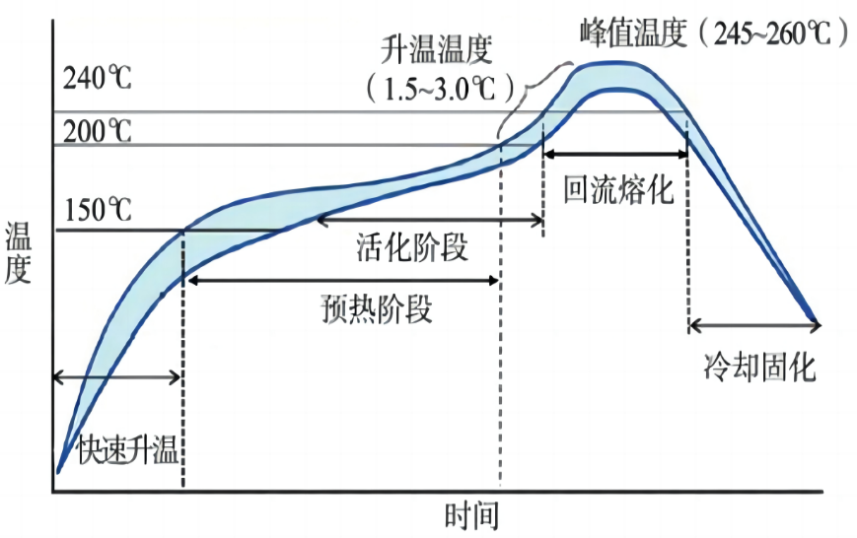
Посилання на профіль для кожної ділянки пайки оплавленням
На етапі попереднього нагріву та активації леткі компоненти флюсу в паяльній пасті будуть випаровуватися в газ при нагріванні. У той же час при видаленні оксиду на поверхні зварювального шару будуть утворюватися гази. Деякі з цих газів випаровуються та залишають пасту, а кульки припою щільно конденсуються через випаровування флюсу. На стадії дефлегмації залишки флюсу в паяльній пасті швидко випаровуються, олов’яні кульки розплавляться, невелика кількість флюсового леткого газу та більша частина повітря між олов’яними кульками не будуть вчасно розсіяні, а залишок у розплавлене олово та під напругою розплавленого олова утворюють гамбургерну сендвічну структуру та захоплюються пайкою друкованої плати та електронними компонентами, а також газ, загорнутий у рідке олово, важко вийти лише завдяки висхідній плавучості Верхній час плавлення дуже короткий. Коли розплавлене олово охолоджується і стає твердим оловом, у зварювальному шарі з’являються пори та утворюються отвори для пайки, як показано на малюнку 3.
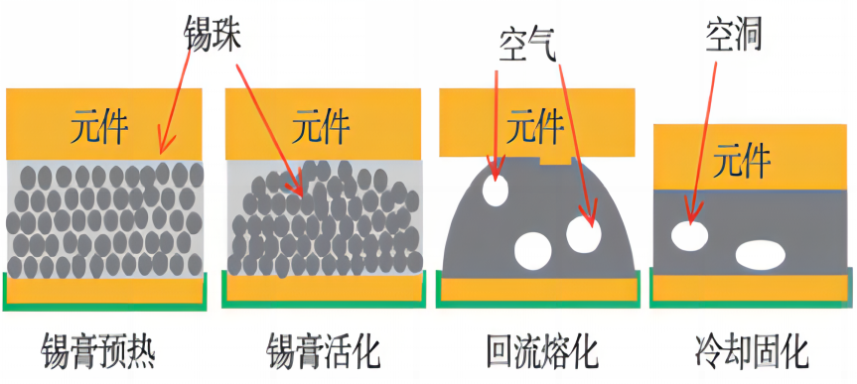
Схематична діаграма пустот, утворених оплавленням паяльною пастою
Основною причиною зварювальної порожнини є те, що повітря або летючий газ, загорнутий у паяльну пасту після плавлення, не виводиться повністю. Фактори впливу включають матеріал паяльної пасти, форму друку паяльної пасти, кількість друку паяльної пасти, температуру дефлегмації, час дефлегмації, розмір зварювання, структуру тощо.
3. Перевірка факторів впливу паяльної пасти для друку оплавленням під зварювання отворів
QFN і випробування на чисту кришку використовувалися для підтвердження основних причин утворення порожнеч під зварюванням оплавленням і для пошуку способів покращення порожнеч під час зварювання оплавленням, надрукованих паяльною пастою. Профіль зварювального продукту для зварювання паяльною пастою QFN і паяльної пасти з голою стружкою показано на малюнку 4, розмір зварювальної поверхні QFN становить 4,4 мм x 4,1 мм, зварювальна поверхня — луджений шар (100% чисте олово); Зварювальний розмір голої мікросхеми становить 3,0 мм х 2,3 мм, зварювальний шар — це напилений нікель-ванадієвий біметалічний шар, а поверхневий шар — ванадій. Зварювальна площадка підкладки була покрита нікель-паладієвим золотом без електроліту, а товщина становила 0,4 мкм/0,06 мкм/0,04 мкм. Використовується паяльна паста SAC305, обладнання для друку паяльної пасти – DEK Horizon APix, обладнання для рефлюксної печі – BTUPyramax150N, а рентгенівське обладнання – DAGExD7500VR.
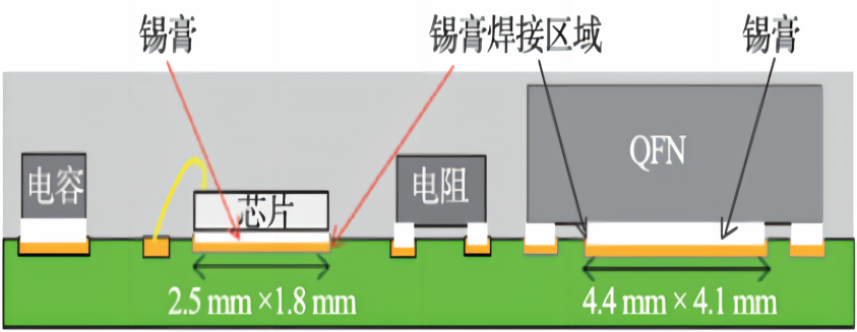
QFN і креслення зварювання голою стружкою
Для полегшення порівняння результатів випробувань зварювання оплавленням було виконано за умов, наведених у таблиці 2.
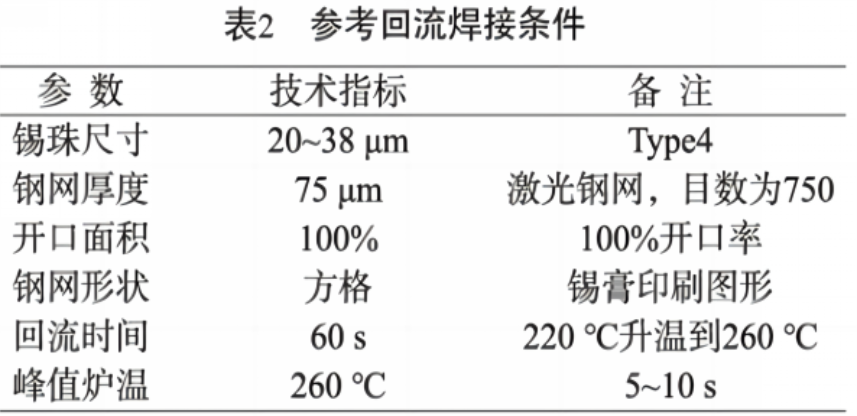
Таблиця умов зварювання оплавленням
Після завершення поверхневого монтажу та зварювання оплавленням зварювальний шар було виявлено за допомогою рентгенівського випромінювання, і було виявлено великі отвори в зварювальному шарі в нижній частині QFN і оголеної стружки, як показано на малюнку 5.
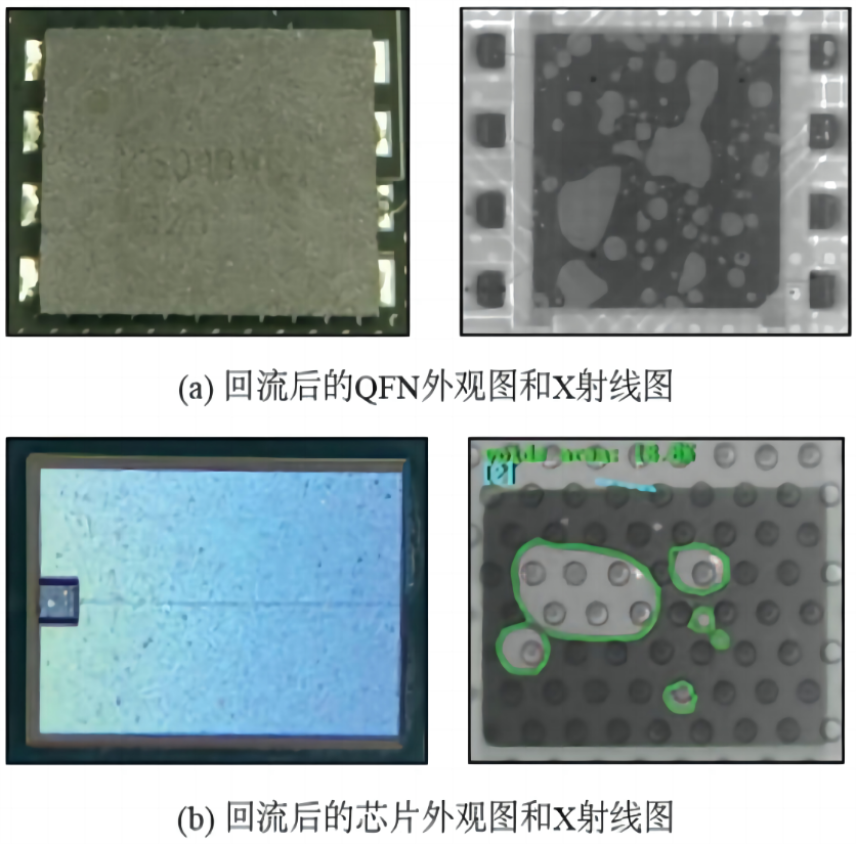
QFN і чіп-голограма (рентгенівський знімок)
Оскільки розмір олов’яного валика, товщина сталевої сітки, швидкість відкриття площі, форма сталевої сітки, час дефлегмації та пікова температура печі впливатимуть на порожнечі під зварювання оплавленням, існує багато факторів впливу, які будуть безпосередньо перевірені випробуванням DOE, а також кількість експериментальних групи будуть занадто великими. Необхідно швидко відібрати та визначити основні фактори впливу за допомогою кореляційного порівняльного тесту, а потім додатково оптимізувати основні фактори впливу за допомогою DOE.
3.1 Розміри отворів для припою та олов’яних кульок паяльної пасти
Під час тестування паяльної пасти типу 3 (розмір кульок 25-45 мкм) SAC305 інші умови залишаються незмінними. Після оплавлення отвори в шарі припою вимірюються та порівнюються з паяльною пастою типу 4. Виявлено, що отвори в шарі припою не відрізняються суттєво між двома видами паяльної пасти, що вказує на те, що паяльна паста з різним розміром кульок не має явного впливу на отвори в шарі припою, що не є фактором впливу, як показано на ФІГ. 6 Як показано.
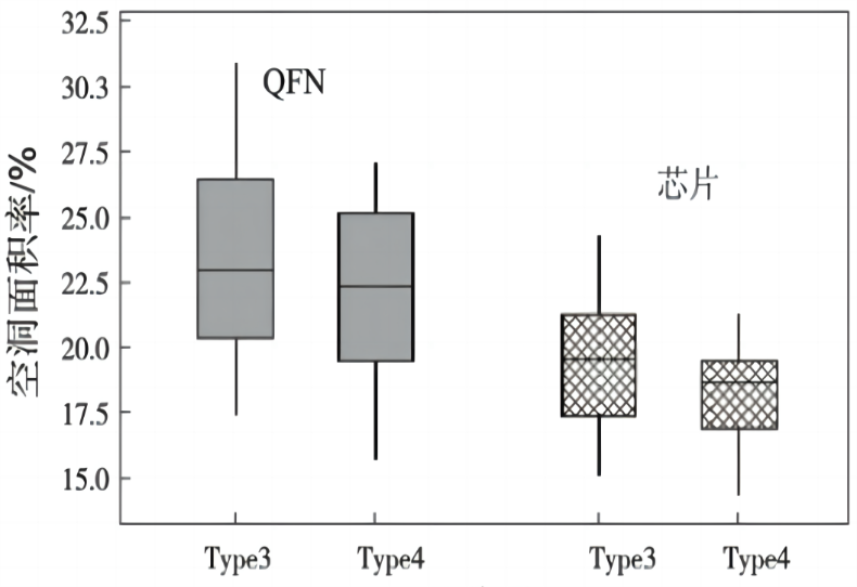
Порівняння отворів порошку металевого олова з різними розмірами частинок
3.2 Товщина зварювальної порожнини та друкованої сталевої сітки
Після оплавлення площа порожнини наплавленого шару вимірювалася друкованою сталевою сіткою товщиною 50 мкм, 100 мкм і 125 мкм, інші умови залишалися незмінними. Було виявлено, що вплив різної товщини сталевої сітки (паяльної пасти) на QFN порівнювався з ефектом друкованої сталевої сітки товщиною 75 мкм. Зі збільшенням товщини сталевої сітки площа порожнини поступово повільно зменшується. Після досягнення певної товщини (100 мкм) площа порожнини зміниться і почне збільшуватися зі збільшенням товщини сталевої сітки, як показано на малюнку 7.
Це показує, що при збільшенні кількості паяльної пасти рідке олово з флегмою покривається мікросхемою, а вихід залишкового повітря вузький лише з чотирьох сторін. Коли кількість паяльної пасти змінюється, випуск залишкового повітря також збільшується, і миттєвий вибух повітря, загорнутого в рідке олово, або летючий газ, що виходить з рідкого олова, спричинить розбризкування рідкого олова навколо QFN і мікросхеми.
Випробування показали, що зі збільшенням товщини сталевої сітки вибух бульбашки, викликаний виходом повітря або леткого газу, також збільшиться, і ймовірність розбризкування олова навколо QFN і стружки також збільшиться відповідно.
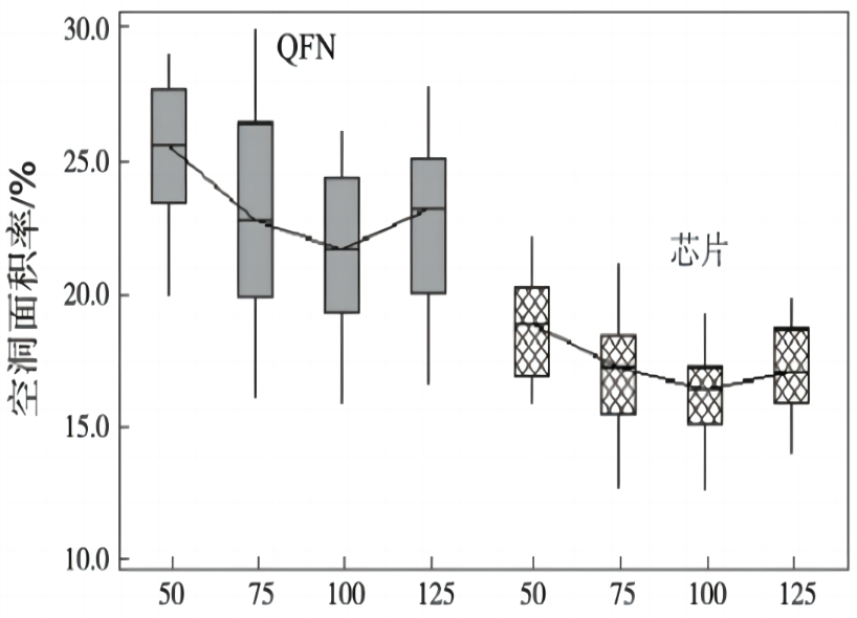
Порівняння отворів у сталевих сітках різної товщини
3.3 Співвідношення площі зварювальної порожнини та отвору сталевої сітки
Було протестовано друковану сталеву сітку зі швидкістю розкриття 100%, 90% і 80%, а інші умови залишилися незмінними. Після оплавлення площа порожнини звареного шару була виміряна та порівняна з надрукованою сталевою сіткою зі 100% швидкістю відкриття. Було виявлено, що не було істотної різниці в порожнині звареного шару за умов швидкості розкриття 100% і 90% 80%, як показано на малюнку 8.
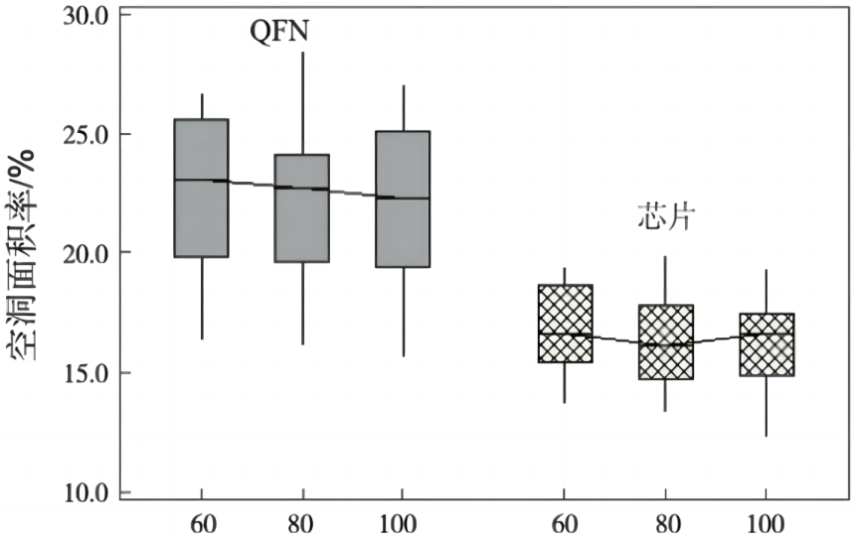
Порівняння порожнин різної площі отвору різної сталевої сітки
3.4 Зварна порожнина та друкована сталева сітка
При випробуванні форми друку паяльної пасти стрічки b і похилої сітки c інші умови залишаються незмінними. Після оплавлення площа порожнини зварювального шару вимірюється та порівнюється з друкованою формою сітки a. Виявлено, що немає істотної різниці в порожнині зварювального шару в умовах сітки, смуги та похилої сітки, як показано на малюнку 9.
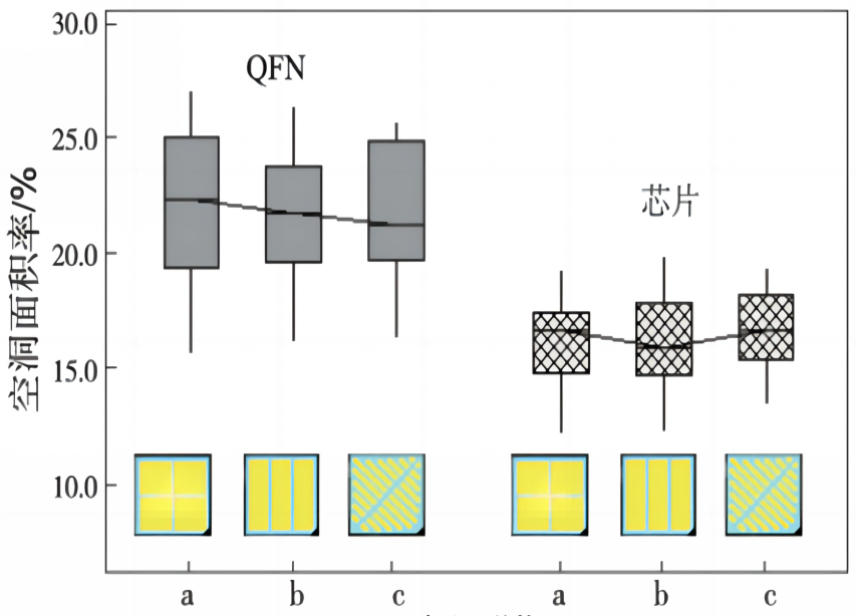
Порівняння отворів у різних режимах відкриття сталевої сітки
3.5 Зварювальна порожнина та час дефлегмації
Після тривалого випробування часу кипіння (70 с, 80 с, 90 с) інші умови залишаються незмінними, отвір у зварювальному шарі вимірювали після кипіння, і порівняно з часом кипіння 60 с було виявлено, що зі збільшенням час кипіння, площа зварювального отвору зменшувалася, але амплітуда зменшення поступово зменшувалася зі збільшенням часу, як показано на малюнку 10. Це показує, що у випадку недостатній час кипіння, збільшення часу зворотного холодильника сприяє повному витоку повітря, загорнутого в розплавлене рідке олово, але після збільшення часу зворотного холодильника до певного часу, повітря, загорнуте в рідке олово, важко перелити знову. Час дефлегмації є одним із факторів, що впливають на зварювальну порожнину.
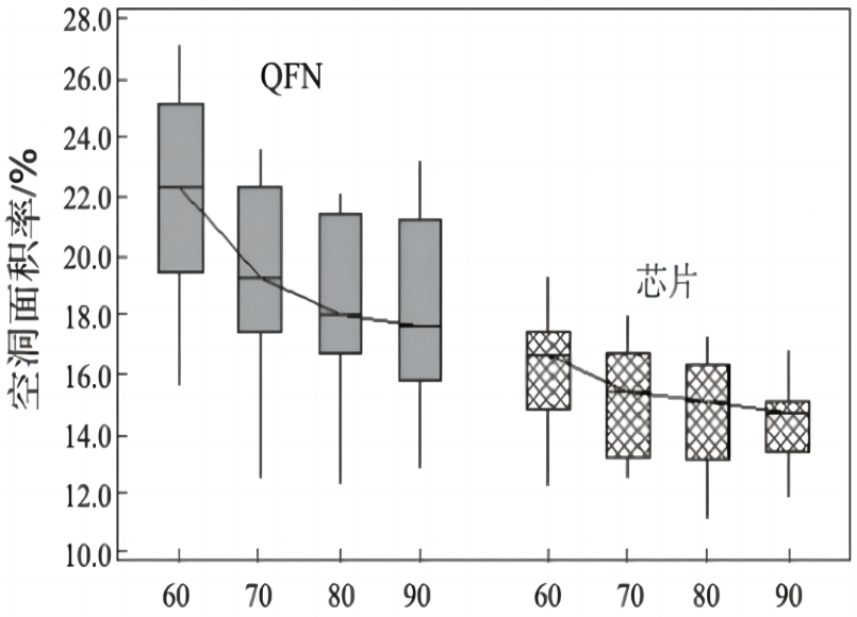
Відповідне порівняння різних тривалостей рефлюксу
3.6 Зварювальна порожнина та пікова температура печі
При випробуванні на піковій температурі печі 240 ℃ і 250 ℃ та інших незмінних умовах площа порожнини звареного шару була виміряна після оплавлення, і порівняно з піковою температурою печі 260 ℃ було виявлено, що за різних умов пікової температури печі порожнина зварений шар QFN і чіп істотно не змінилися, як показано на малюнку 11. Це показує, що різна пікова температура печі не має явного впливу на QFN і отвір у зварювальному шарі чіпа, що не є фактором впливу.
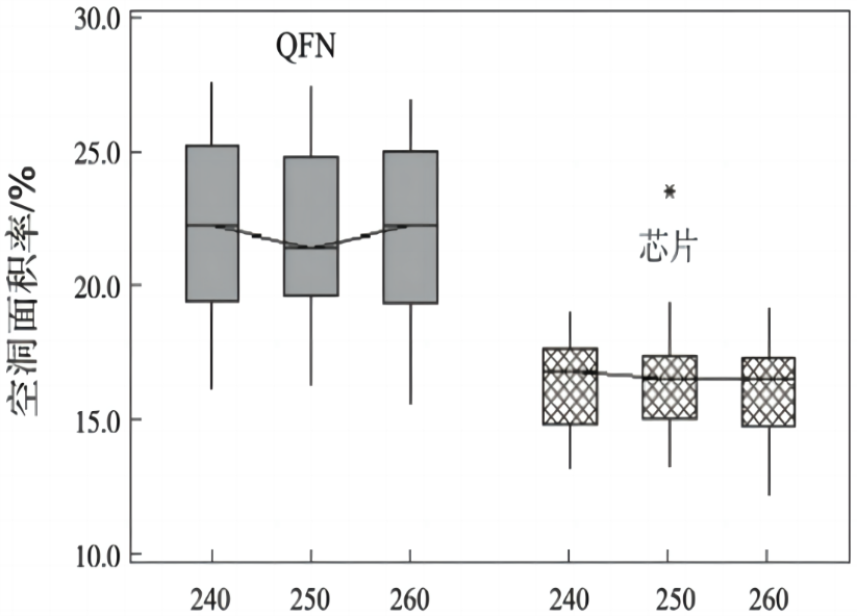
Недійсне порівняння різних пікових температур
Наведені вище випробування вказують на те, що суттєвими факторами, які впливають на порожнину зварного шару QFN і стружки, є час кипіння та товщина сталевої сітки.
4 Покращення зварювальної порожнини оплавленням друку паяльною пастою
4.1 Тест DOE для покращення зварювальної порожнини
Отвір у зварювальному шарі QFN та стружки було покращено шляхом знаходження оптимального значення основних факторів впливу (часу флегми та товщини сталевої сітки). Паста була SAC305 типу 4, форма сталевої сітки була типу сітки (ступінь розкриття 100%), пікова температура печі була 260 ℃, а інші умови випробувань були такими ж, як і для випробувального обладнання. Випробування DOE та результати наведені в таблиці 3. Вплив товщини сталевої сітки та часу кипіння на QFN та зварювальні отвори для стружки показано на малюнку 12. Завдяки аналізу взаємодії основних факторів впливу виявлено, що використання сталевої сітки товщиною 100 мкм і час дефлегмації 80 с може значно зменшити зварювальну порожнину QFN і стружки. Швидкість зварювальної порожнини QFN зменшується з максимальних 27,8% до 16,1%, а швидкість зварювальної порожнини стружки зменшується з максимальних 20,5% до 14,5%.
Під час випробування було виготовлено 1000 продуктів за оптимальних умов (товщина сталевої сітки 100 мкм, час кипіння 80 с), а швидкість зварювальної порожнини 100 QFN і стружки вимірювалися випадковим чином. Середня частота зварювальних порожнин QFN становила 16,4%, а середня частота зварювальних порожнин стружки становила 14,7%. Швидкість зварювальних порожнин стружки та стружки явно зменшилася.
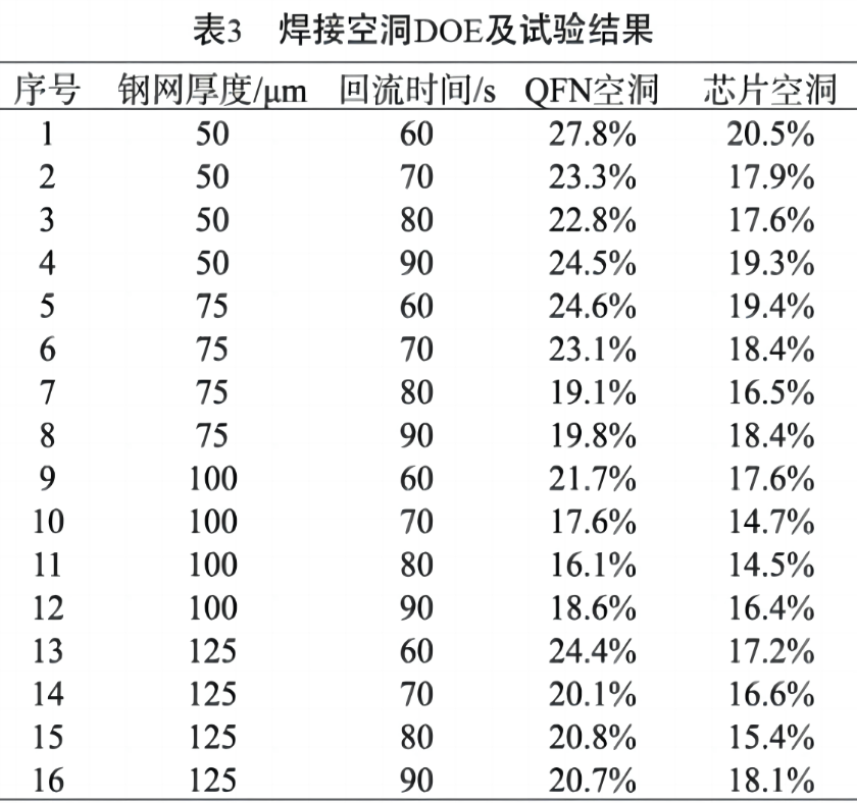
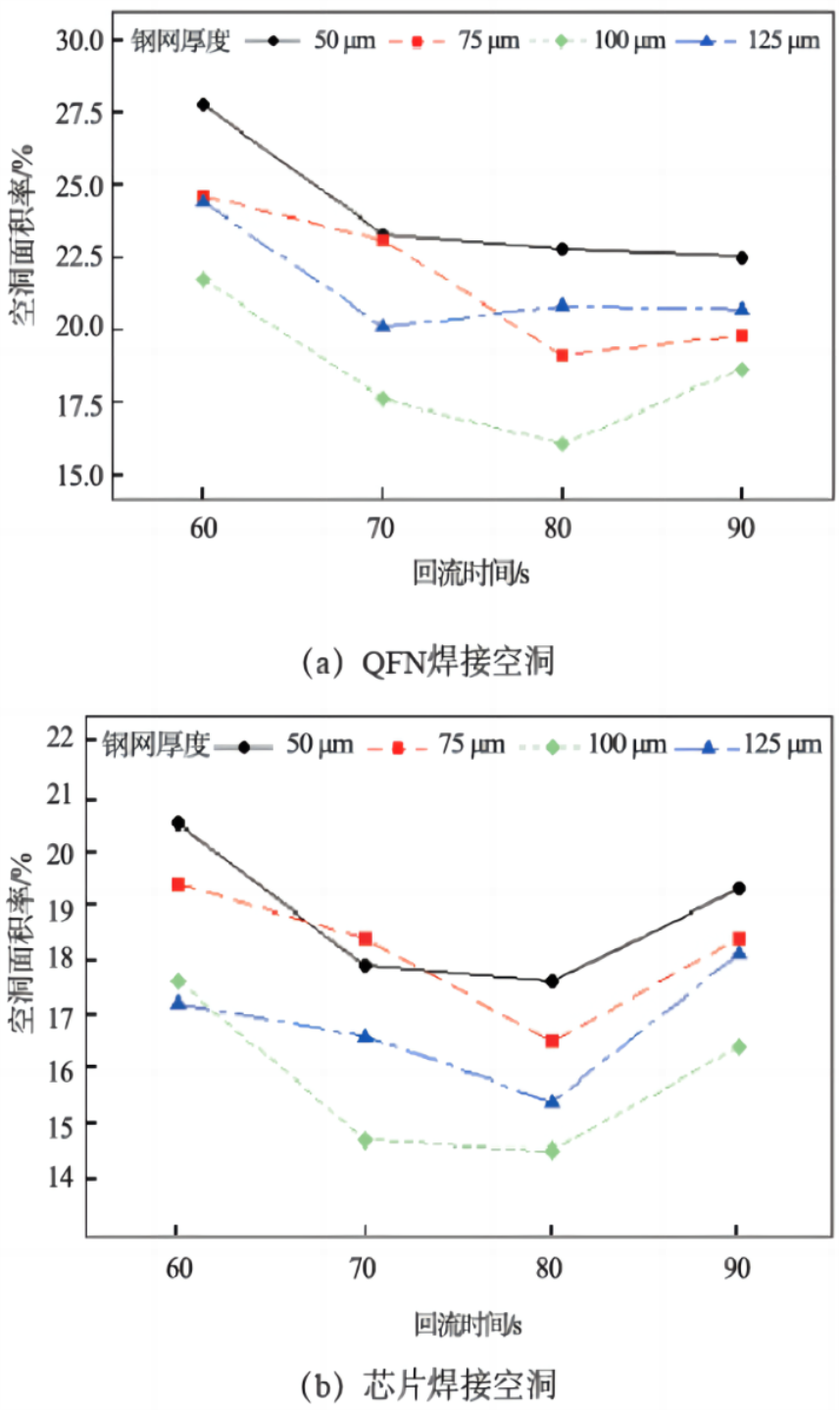
4.2 Новий процес покращує зварювальну порожнину
Фактична виробнича ситуація та випробування показують, що коли площа зварювальної порожнини в нижній частині мікросхеми становить менше 10%, проблема розтріскування порожнини мікросхеми не виникне під час склеювання свинцю та формування. Параметри процесу, оптимізовані DOE, не можуть відповідати вимогам аналізу та вирішення отворів під час звичайного зварювання оплавленням паяльною пастою, тому площу зварювальної порожнини мікросхеми потрібно ще зменшити.
Оскільки чіп, покритий припоєм, запобігає виходу газу з припою, кількість отворів у нижній частині чіпа ще більше зменшується шляхом усунення або зменшення газу, покритого припоєм. Застосовується новий процес зварювання оплавленням із двома друками паяльною пастою: один друк паяльною пастою, один оплавленням, що не покриває QFN, і чистим чіпом, що випускає газ у припій; Специфічний процес друку вторинної паяльної пасти, латки та вторинного флегмування показано на малюнку 13.
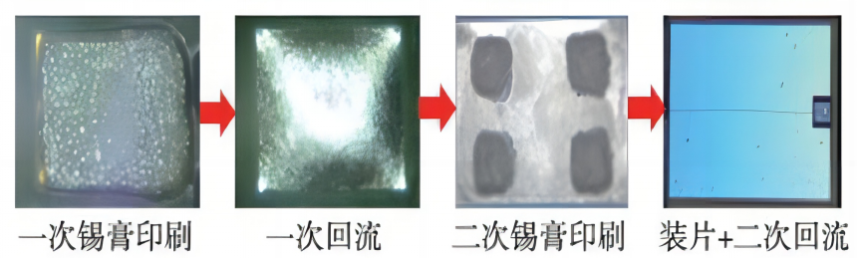
Коли паяльна паста товщиною 75 мкм друкується вперше, більша частина газу в припої без покриття мікросхеми виходить із поверхні, а товщина після кипіння становить близько 50 мкм. Після завершення первинного флегмування на поверхні охолодженого затверділого припою друкуються квадратики (щоб зменшити кількість паяльної пасти, зменшити кількість витікання газу, зменшити або усунути розбризкування припою) і паяльну пасту з товщина 50 мкм (наведені вище результати тесту показують, що 100 мкм є найкращим, тому товщина вторинного друку становить 100 мкм.50 мкм=50 мкм), потім встановити мікросхему, а потім повернутися через 80 с. У припої майже немає отвору після першого друку та оплавлення, а паяльна паста під час другого друку мала, а отвір під зварювання невеликий, як показано на малюнку 14.
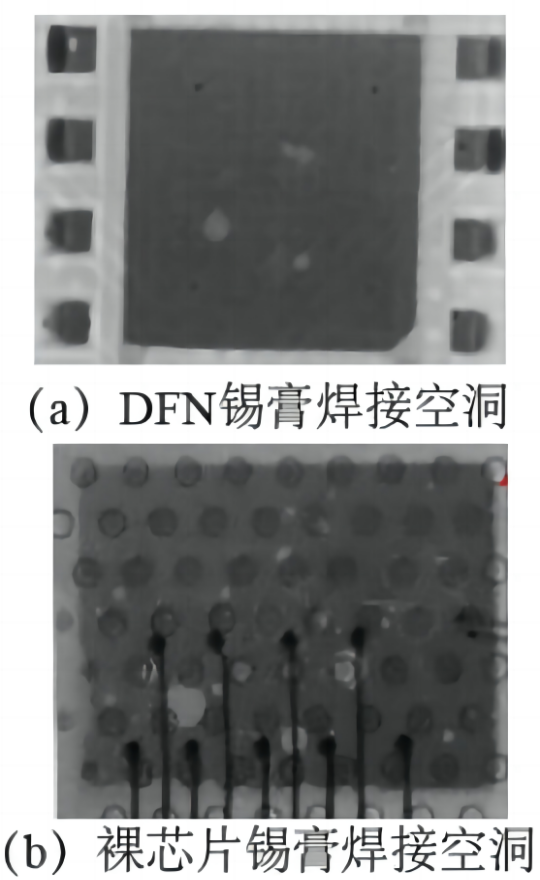
Після двох відбитків паяльної пасти малюнок пустоти
4.3 Перевірка ефекту зварювальної порожнини
Виробництво 2000 виробів (товщина сталевої сітки для першого друку становить 75 мкм, товщина сталевої сітки для другого друку становить 50 мкм), інші умови без змін, випадкове вимірювання 500 QFN і швидкість зварювання стружки показали, що новий процес після першого зворотного холодильника немає порожнини, після другого зворотного холодильника QFN Максимальна швидкість зварювання порожнини 4,8%, а максимальна швидкість зварювальної порожнини чіпа становить 4,1%. Порівняно з оригінальним процесом зварювання однопастним друком і оптимізованим процесом DOE, зварювальна порожнина значно зменшилася, як показано на малюнку 15. Після функціональних випробувань усіх виробів не виявлено тріщин.
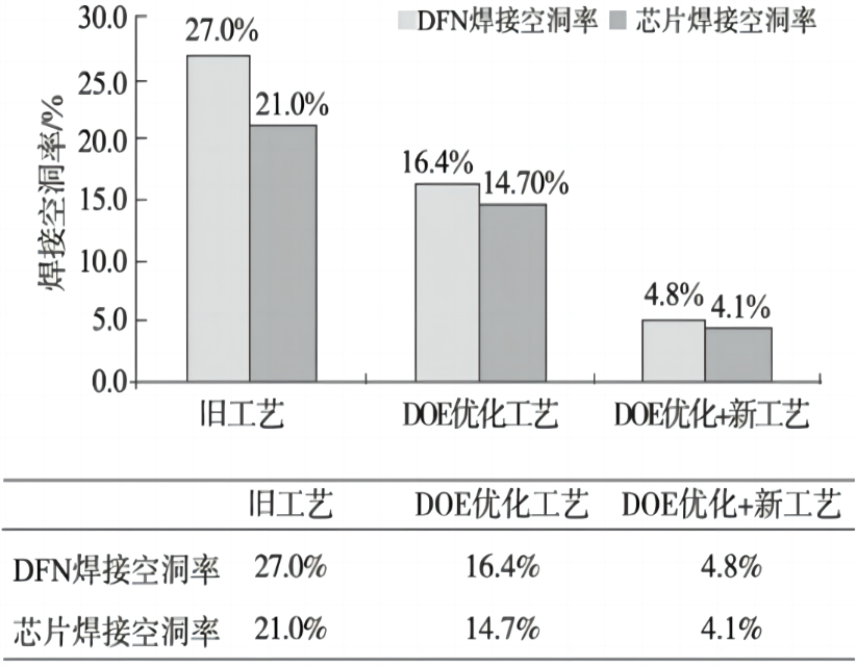
5 Підсумок
Оптимізація кількості друку паяльної пасти та часу дефлегмації може зменшити площу зварювальної порожнини, але швидкість зварювальної порожнини все ще велика. Використання двох методів зварювання оплавленням з паяльною пастою може ефективно та максимально збільшити швидкість зварювальної порожнини. Площа зварювання чистого чіпа схеми QFN може становити 4,4 мм x 4,1 мм і 3,0 мм x 2,3 мм відповідно в масовому виробництві. Швидкість порожнини при зварюванні оплавленням контролюється нижче 5%, що покращує якість і надійність зварювання оплавленням. Дослідження в цій статті є важливою довідкою для вирішення проблеми зварювальної порожнини великої площі зварювальної поверхні.
Час публікації: 05 липня 2023 р